お問い合わせの多いFPC実装(フレキシブル基板)についてシリーズ化して紹介をしていこうと思います。
それでは、早速FPC基板実装シリーズ第1弾の「個片FPCの実装方法」ついて書いていきたいと思います。
FPC実装は、通常のリジット基板(FR-4やCEM3)と比較すると実装方法が異なります。是非ご参考にしてください。 以下、フレキシブル基板=FPCと略して記載します。
また、今回は、今後投稿を予定しているFPC実装の設計留意点と紐付けをしたいと思います。個片実装時に問題になってくる認識マーク(BOCマーク)がない場合に、起こる不具合についても触れていきます。
・個片FPCとは?
そもそも今回説明をする「個片FPC」とはどのようなものなのでしょうか?
通常のプリント基板と同様に、FPCにはシート上に面付けされた「シート・キット」形状のものと、面付けされていない「個片」のものが存在します。通常のプリント基板でいうところの「捨て基板がない製品単体のFPC」を当社では「個片FPC」と呼んでいます。
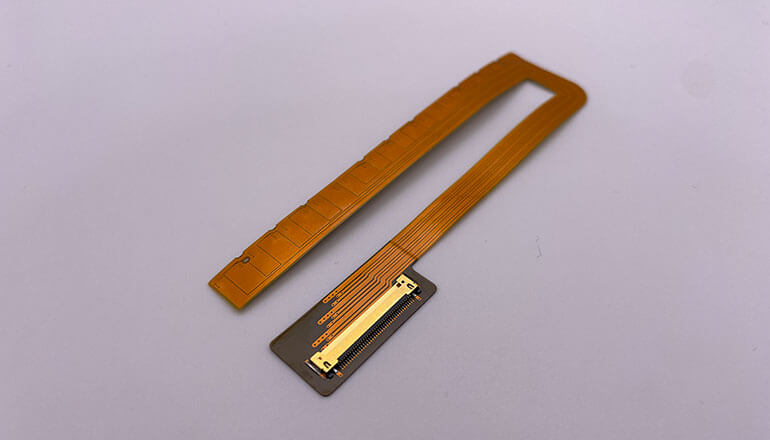
シート上のFPCの場合、部品実装後に個片にカットするとなると型抜きを行う必要があります。
部品がはんだ付けされた状態での型抜きは、部品やはんだ付け箇所に応力がかかることから、そのリスクを考慮して個片の状態で実装するケースがあるわけです。当社では、実装しているものは、この個片FPCの割合が圧倒的に多く、シート状ので実装するものは、数量の多い量産案件に限っています。
・個片FPCの実装工程は?
それでは、個片FPCの実装方法を工程順に見てみましょう。
工程1 : 予備乾燥(FPCのベーキング)
FPCを乾燥させ、吸湿している水分を取り除きます。
これは、はんだ付けの工程で高温に晒された際に、FPCの不具合発生を防止する大切な工程です。
FPCのカバーレイやベースフィルムに使用されているポリイミドは非常に吸湿しやすい材料です。通常のエポキシ系のリジット基板と比較すると、10倍ほど吸湿しやすく、吸湿をすることで耐熱性も低下してしまいます。また補強板の取り付けられたFPCの場合、補強板を貼り付けている接着材も吸湿をするため、乾燥工程を怠るとFPCや補強板内の膨れ、気泡の発生や導体の剥がれ・めくれといった不具合につながってしまいます。下記にFPCの構成や補強材料による、必要な乾燥温度と乾燥時間を表にまとめてみました。
基板種類 | 構成 | 補強材料 | 乾燥温度 | 乾燥時間 |
---|---|---|---|---|
FPC | 片面 | なし | 80°C | 30分以上 |
フィルム | 80°C | 1時間以上 | ||
ガラスエポキシ | 120°C | 1時間以上 | ||
両面 | なし | 120°C | 30分以上 | |
フィルム | 120°C | 1時間以上 | ||
ガラスエポキシ | 120°C | 1時間以上 |
(ベーキング条件:JPCA-DG02-2006に準ずる)
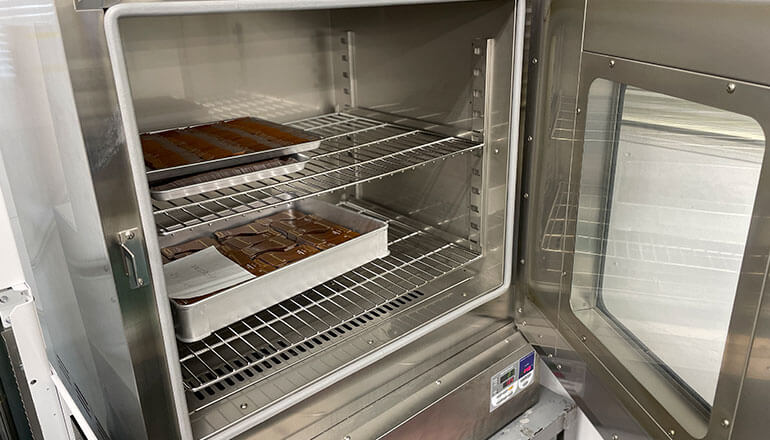
工程2 : キャリアボードへの貼り付け
粘着性のあるキャリアボードにFPCを整列させます。整列をさせることで、自動機を使用して実装することが可能になります。今回は外形基準で整列させるケースを紹介します。
粘着ボードに整列用のSUSプレートを重ね合わせ、FPCを貼っていきます。
片面実装のFPCであれば、当社の汎用粘着ボードで実装することができます。250mm*200mmサイズのボードを500枚程度保有しています。両面実装FPCの場合、原則、片面の実装された部品との干渉を避けた専用のキャリアボードを制作する必要があります。このボードは耐熱性が高く、このままリフロー炉へ入れることができます。
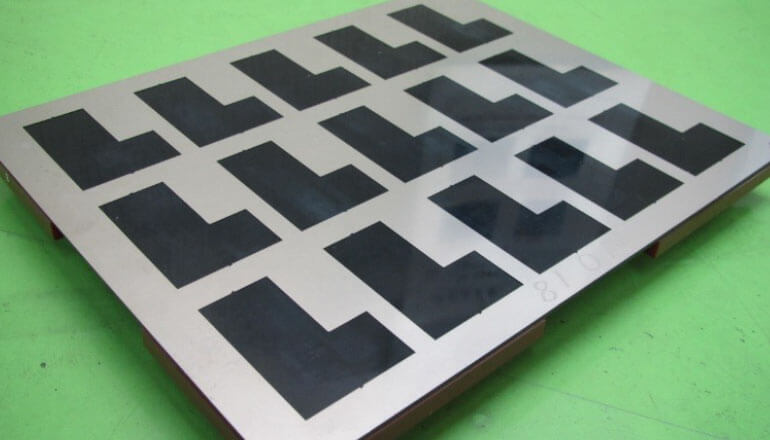
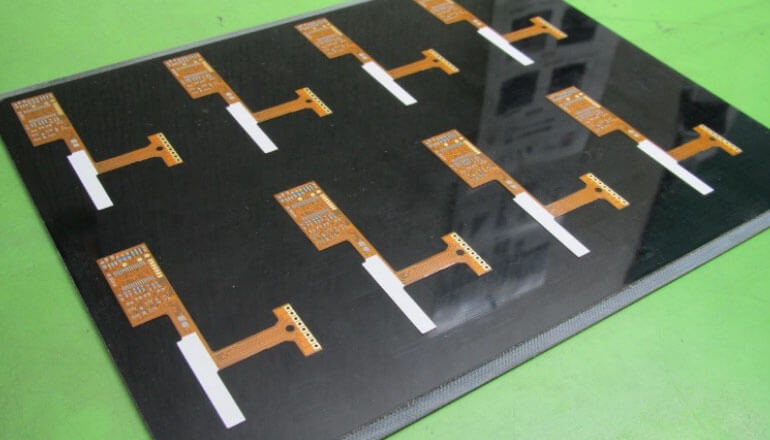
工程3 : はんだペースト印刷
キャリアボードに貼り付けたFPCに、はんだペーストを印刷していきます。自動機で印刷する場合は、基板に配置された「認識マーク」を自動機がカメラで認識し、位置合わせを行なっていきます。キャリアボードへの貼り合わせの精度が出ない場合は1枚ずつ印刷を行なった後に、キャリアボードに貼り合わせるケースもあります。試作や少量であれば自動機を使用せずマニュアルで印刷を行うこともできます。粘着ボードに貼られたFPCのはんだペースト印刷は、リジット基板へのはんだペースト印刷と比較すると印刷量が多くなる傾向があります。メタルマスクの厚さ・開口条件は粘着キャリアボード用に考慮する必要があります。
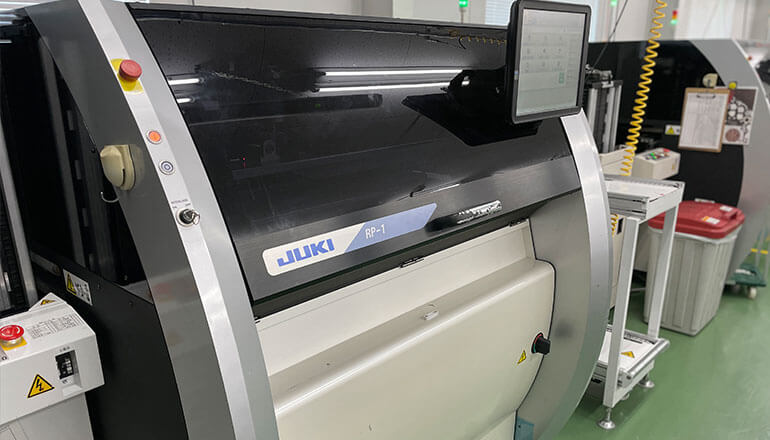
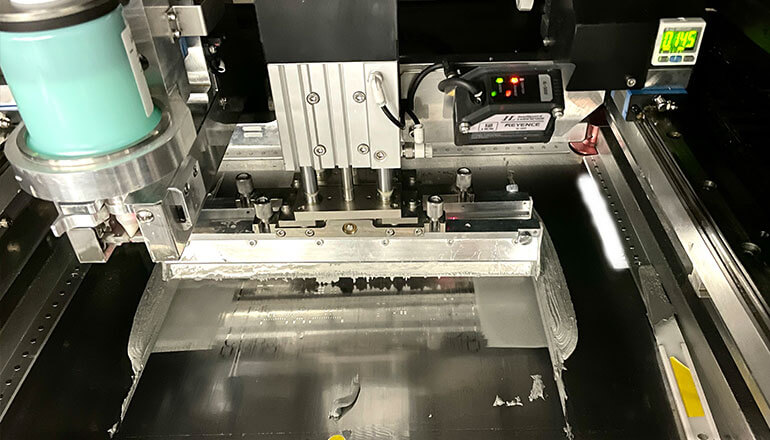
注意事項
・個片FPCは外形基準で貼っているため、その貼り精度によって印刷精度が落ちてしまいます。
精度を必要とする微小部品実装や狭ピッチ実装、安定性の必要な量産実装はシート形状のFPCで実装をすることをオススメします。
・また、自動機を使用し、印刷・実装精度を最大限に引き出すためには認識マーク(BOCマーク)が必須です。
工程4 : 部品搭載
FPCに部品を搭載します。貼り付けられた個々のFPCに認識マークがあれば工程2で貼りズレがあったとしても、搭載精度を保ちリジット基板と同様に実装することができます。逆に、認識マークを設けていないものは、搭載精度が出ません。シルク印刷や他のもので認識を取らざるを得ない場合もあるのですが、正直精度は出すことができません。基板の製造工程において、部品を搭載するランドと同一工程で作られた認識マーク(BOCマーク)が必要となります。スクリーン印刷やインクジェットで印刷されたシルクなどは、部品ランドとは別のデータ・工程で作られており、位置精度は期待できません。高精度を謳っている最新設備の精度を発揮することができないことから認識マークを設けないことは、品質的にも、実装コスト的にもデメリットしかないのです・・・。下記の写真は認識マークがないFPCに部品を自動機実装した画像です。一見わからないかもしれませんが、チップ部品などの位置精度が全体的に出ていません。
また、FPCの場合、リジット基板と比べて厚さが薄いためコネクタのボスなど裏側に飛び出す部品がある場合は注意が必要です。キャリアボードに座繰りや穴を設けて逃げをつくる必要があります。はんだ印刷と同様に認識マークがないFPCなどは、少量・試作であれば手作業で部品搭載も可能です。
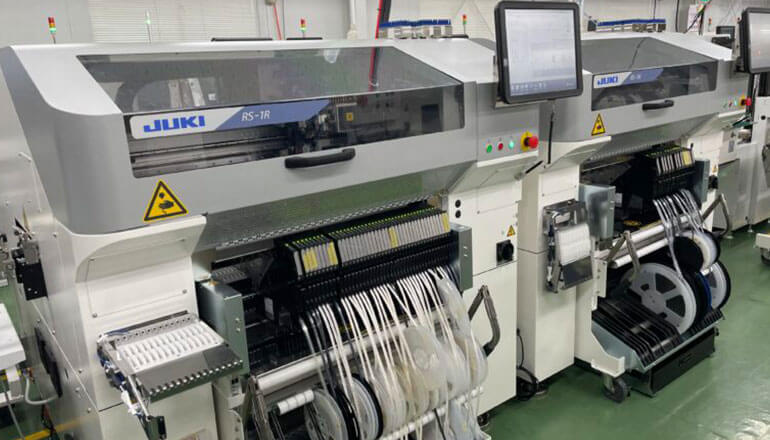
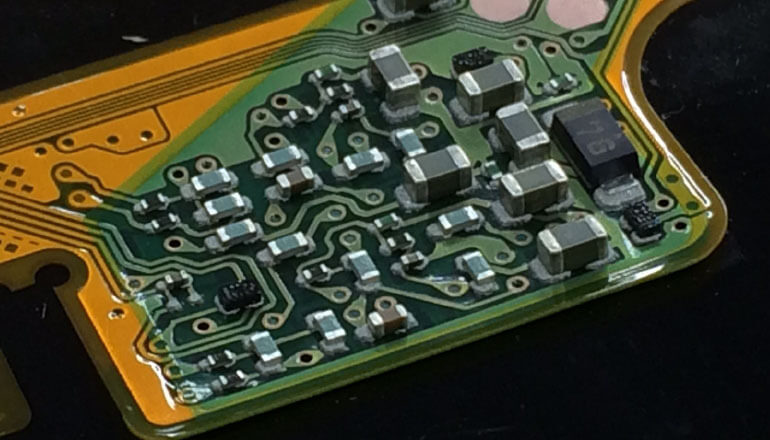
工程5 : リフロー炉によるはんだ付け
N2リフロー炉ではんだ付けを行います。キャリアボードも考慮に入れた温度プロファイルではんだを溶融させてはんだ付けを行なっていきます。FPCの場合、このリフロー炉についても注意が必要です。FPC・補強板・接着材の組み合わせやグランドパターンの入り方によってFPCが大きく反ることがあります。粘着性キャリアボードには「強粘着」と呼ばれている粘着性が強いものもご用意していますが、それでも反りを抑えることができないくらい強い反りが出ることがあります。反りが出てしまうとBGAやLGAなどが接続不良につながるだけでなく、粘着キャリアボードから剥がれリフロー内の空気の対流で飛ばされてしまうような事故が起こります。
実際に試作を行わないと事前に反り具合を把握することが難しいケースも多いと思います。
反ってしまうFPCに対しては、無理に粘着に貼り付けることでFPCの膨張の逃げがなくなり、一層反りが悪化してしまうケースがあります。このようなケースでは「磁性治具」と呼んでいるマグネットを使用してFPCを挟み込むような特殊なキャリアボードを制作し対応します。
下記写真は、認識マークがないFPCに部品実装したものをリフローしたものです。部品搭載位置精度が出ていないことで、赤矢印の部品は、チップのずれや立ちが多発しています。
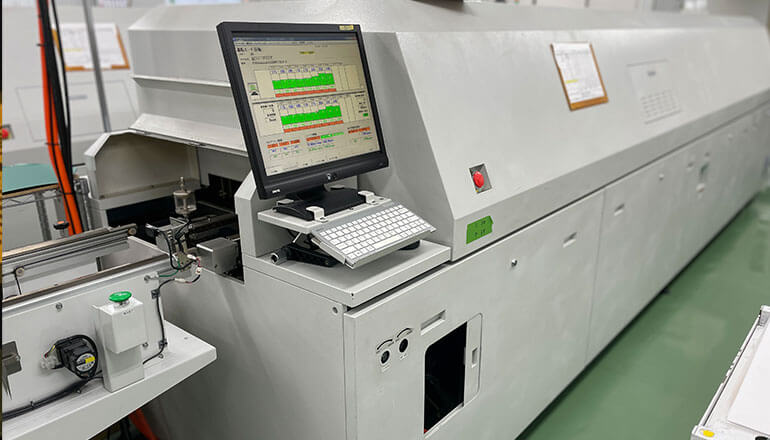
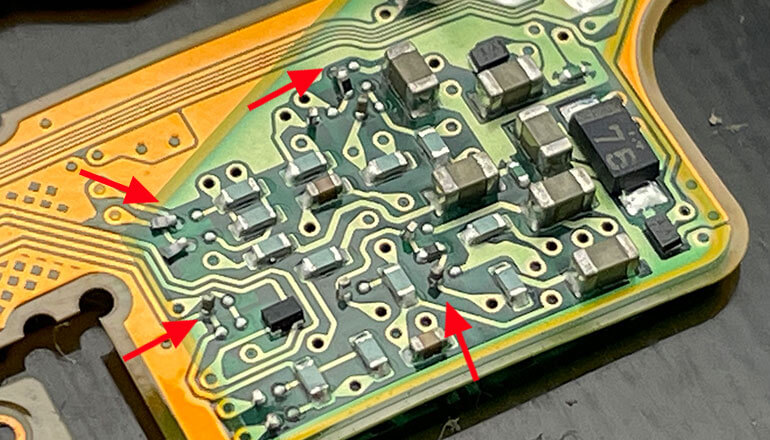
はんだ付け後の不具合(チップ立ち・ずれ)
<両面実装の場合は、工程2−4をもう1度繰り返します。裏面実装がある場合は専用キャリアボードが必要です。>
工程6 : 外観検査・X線検査
実装後は、製品の仕様によって画像検査装置(AOI)による検査、目視検査、X線検査を行います。これまでの工程で記載した通りFPCの場合、リジット基板と比較すると不具合発生率は必然とUPしてしまいます。そこで当社では、実装条件が揃っていないFPCについては常にダブルチェック(1次検査・2次検査)を設けることで検査における検出能力を高めています。AOIの使用については、専用キャリアボードの有無や用意できる枚数に応じて異なりますのでご相談ください。
工程7 : 梱包・出荷
検査を終えたFPCは静電袋もしくは、専用トレイに収納しお客様へ発送いたします。台数が多い機種は、専用トレイを制作されることをおすすめいたします。当社で汎用トレイの選定や専用トレイの制作も承ります。
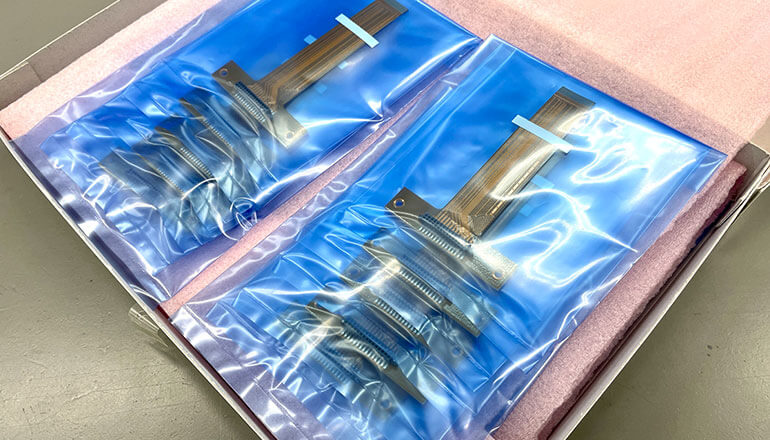
今回は個片FPCの実装方法・工程について記事にしてみました。引き続きFPC実装についての記事をシリーズでお届けする予定です。
次回は、FPCの個片基板・シート形状の際の認識マーク・BADマークについてブログをお届けいたします。ご期待ください。
投稿者プロフィール

-
ビックライズ代表取締役COO。
提案のできる会社を目指し、日々奮闘しています。
これまでの経験、実績から「役立つ内容のブログ」をテーマに配信していきます。
最新の投稿
ブログ2025.02.04FPC基板実装:④補強板とキャリアボード
ブログ2022.06.01FPC基板実装:③キャリアボードの種類について(メリット・デメリット)
ブログ2022.04.08FPC基板実装:②FPCの認識マーク、BADマーク
ブログ2022.03.25FPC基板実装:個片FPCの実装方法について